Textile Industries
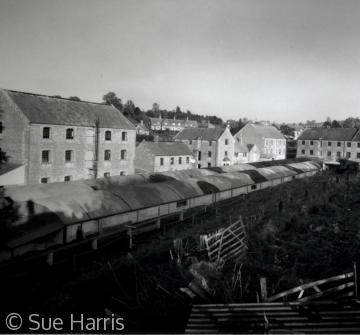
Many animal and plant fibres can be made into woven fabric. The processes differ for each but broadly consist of cleaning and preparing, spinning, or throwing in the case of silk, weaving, and finally colouring and finishing off by stretching, trimming, pressing, felting or raising the nap according to fabric type.
Weaving is a prehistoric craft but during the later Middle Ages England became famous for woollen cloth especially the broadcloth woven on looms twice the traditional width. The early industry was organised in and around certain towns with spinners, weavers, dyers, fullers, tuckers and shearmen. Stroud, Gloucestershire, Dunster and Taunton in Somerset, and Kersey in Suffolk had cloths named after them in the early modern period. Merchants later called clothiers often managed the entire process from buying wool to selling cloth. In some areas these men were called woolcombers, presumably because they prepared worsted wool by combing before putting it out for spinning.
From the late 16th century attempts were made to bring weavers into large workshops or factories, notably by ‘Jack of Newbury’. In the 18th century the many inventions that led to the Industrial Revolution gave rise to the financing and building of large water and steam-powered woollen mills, increasing productivity and driving down the price of cloth. Despite resistance by independent handloom weavers, in the later 19th century, when carding and combing machines were introduced, all the processes for producing woollen cloth had been mechanised. Although sheep wool was the most usual, cloth was also made from goat hair, notably cashmere, imitated at Norwich with a wool and silk substitute. Alpaca was sometimes used, especially at Bradford, Yorkshire.
Linen production was more difficult to mechanise as flax requires scotching, removing the straw, and retting, soaking until everything except the linen fibre has decomposed. Linen cloth was made in the damper areas of Wales, Scotland and especially Northern Ireland. Most English linen was coarse canvas and fine linen was imported. The Napoleonic wars and bounties for production led to a growth in linen sail making especially in south Somerset and west Dorset. In the 19th century some finer linen for clothing and household furnishings was produced in England, notably at Knaresborough in Yorkshire.
The cotton industry employed thousands of people in mills in the north of England from the later 18th to the later 20th centuries and stimulated the building of canals and railways. Lancashire was the centre of the industry, which also prefers a damp atmosphere. Cotton cloth, often called calico, was normally printed, usually with colourful floral patterns. Manchester was the home of calico printing but the industry was also found in Burnley, Lancashire and in Glasgow. Cotton not only replaced the more expensive silk and linen for clothing and furnishings but was also used for glove manufacture in Ledbury, Herefordshire and for stocking making at Gloucester and Nottingham.
Silk cloth was expensive and its manufacture required patient, delicate handling but from the 18th century it became more affordable even by the middle classes as English and Scottish production increased. Unlike other raw materials it was light and cheap to transport and so was taken to places where there were plentiful supplies of water and cheap labour, usually young girls. The silk was reeled and thrown, the yarn taken away to London or elsewhere for dyeing and brought back for weaving, and the cloth returned for finishing. In the early 19th century many places in the western half of England had silk mills from Ormskirk in Lancashire to Dulverton in Somerset, although they were usually short lived. In Taunton in Somerset and Macclesfield in Cheshire the industry survived longer. Young women would purchase silk thrums, the waste threads from the loom, and weave ribbons at home.
Horsehair cloth is one of the more unusual textiles, also reliant at first on the nimble fingers of very young girls. It dates from an era when thousands of horsetails, trimmed from carriage and cart horses for safety reasons, were available to make an almost indestructible fabric. It was used for upholstery as it resists abrasion, for railway blinds because it does not warp with heat, and for webbing because it is extremely strong. It was the last textile industry to be mechanised and powered looms are not much more productive than handlooms. The only surviving mechanised horsehair industry is at Castle Cary in Somerset, the last horsehair factory in Britain. Not surprisingly horsehair cloth today is many times more expensive than silk.
Other fibres were woven including jute, hemp, sisal or other animal hairs but they were used mainly for hessian and sackcloth, also made in Castle Cary, and at Tetbury in Gloucestershire and Dundee in Scotland.